НАУКОВО-ДОСЛІДНА ЛАБОРАТОРІЯ «ПОЛІМЕРНІ КОМПОЗИТНІ МАТЕРІАЛИ У СУДНОБУДУВАННІ»
(новітнє устаткування для дослідження у комплексі адгезійних, механічних, теплофізичних властивостей, корозійної і зносостійкості, а також структури полімерних композитів)
Мета діяльності:
– встановити основні закономірності впливу енергетичних полів і природи наповнювачів на механізм структуроутворення полімерних композитів і видати рекомендації щодо створення на їх основі функціональних покриттів для захисту технологічного обладнання від корозії та зносу;
– пошук, перевірка робочих гіпотез про зв’язок структури з основними фізико-механічними та теплофізичними властивостями композитів і розробка програмного забезпечення для їх перевірки чисельними методами. Результатом розробок має стати можливість прогнозування за прийнятною для практики точністю однієї або декількох властивостей композитів на підставі відомостей про інші, які досить добре досліджені.
Науковий керівник лабораторії, д.т.н., професор Букетов Андрій Вікторович | Завідувач лабораторією, старший викладач Алексенко Віктор Леонідович |
Команда:
- Д.т.н., професор, академік Академії інженерних наук України, академік ПТАН України, заслужений діяч науки і техніки України, Лауреат Державної премії України, завідувач кафедри транспортних технологій та механічної інженерії ХДМА Букетов Андрій Вікторович – керівник лабораторії.
- Алексенко Віктор Леонідович, старший викладач кафедри транспортних технологій та механічної інженерії, завідувач лабораторії.
- Д.т.н., професор кафедри транспортних технологій та механічної інженерії ХДМА Сапронов О.О.
- Д.т.н., професор, професор кафедри транспортних технологій та механічної інженерії ХДМА Шарко O.B.
- Д.т.н., професор, професор кафедри транспортних технологій та механічної інженерії ХДМА Клевцов K.M.
- Д.т.н., професор, професор кафедри комп’ютерно-інтегрованих технологій ТНТУ ім. І. Пулюя Стухляк П.Д.
- К.т.н., доцент, докторант, доцент кафедри транспортних технологій та механічної інженерії ХДМА Браїло М.В.
- К.т.н., докторант при кафедрі транспортних технологій та механічної інженерії Букетова Н.М.
- К.т.н., доцент, доцент кафедри транспортних технологій та механічної інженерії ХДМА Акімов О.В.
- К.т.н., доцент, доцент кафедри експлуатації суднових енергетичних установок Богдан Ю.О.
- К.т.н., доцент, начальник Морського коледжу ХДМА Гусєв В.М.
- К.т.н., науковий співробітник наукової групи при кафедрі транспортних технологій та механічної інженерії Лещенко О.В.
- К.т.н., науковий співробітник наукової групи при кафедрі транспортних технологій та механічної інженерії Нігалатій В.Д.
- Доктор філософії, старший викладач кафедри природничо-наукової підготовки Якущенко С.В.
- Доктор філософії, cтарший викладач кафедри транспортних технологій та механічної інженерії Сметанкін С.О.
- Асистент кафедри транспортних технологій та механічної інженерії Богдан А.П.
- Аспірант Сапронова А.В.
- Аспірант Кулініч А.Г.
- Аспірант Кулінич В.Г.
- Аспірант Юренін К.Ю.
- Аспірант Соценко В.В.
- Аспірант Антоніо Бертем Да Глорія Де Деуш
- Аспірант Бабій К.А.
- Аспірант Житник Д.В.
- Аспірант Чернявська Т.В.
Наукове та практичне спрямування діяльності:
- розробка нових технологій і матеріалів з підвищеними експлуатаційними характеристиками для захисту корпусів суден;
- дослідження впливу фізичних полів на властивості композитних матеріалів;
- нанокомпозити та нанотехнології в сучасній промисловості;
- використання інформаційних технологій при моделюванні складних систем та прогнозуванні їх властивостей.
Завдання дослідження:
- розробити методологічні підходи до дослідження впливу енергетичних полів (магнітного, ультразвукового, ультрафіолетового випромінювання) на властивості полімерних композитів;
- встановити механізми міжфазової взаємодії дисперсних і волокнистих наповнювачів з полімерним зв’язувачем на нано-, мікро- і макрорівнях;
- дослідити вплив природи наповнювача на характеристики структури зовнішніх поверхневих шарів на межі розділу фаз «полімер – наповнювач» (густина, ступінь зшивання, геометричні розміри);
- видати рекомендації щодо створення на основі розроблених композитів захисних покриттів різного функціонального призначення та здійснити їх впровадження в промисловість.
На сьогодні лабораторія забезпечена сучасним технологічним обладнанням для дослідження структури: ЕПР- і ІЧ-спектроскопія, прилад Товарова, прилад Сокслета; фізико-механічних властивостей: розривна машина, установка для дослідження матеріалів на згинання; реологічних (ротаційний віскозиметр), теплофізичних (теплостійкість, ДТА, ДТГ, ТКЛР, діелектричні характеристики) властивостей, корозійної (імпедансна спектроскопія) і зносостійкості (машина тертя). Додатково є можливість попереднього оброблення композицій при формуванні матеріалів ультразвуком (прилад УЗДН-1500), магнітним полем та ультрафіолетовим опроміненням.
Ідея інновації
Ідеєю проектів є дослідження впливу фізичної природи нано-, мікро- і макродисперсних наповнювачів та дискретних волокон, магнітної обробки, ультразвукового та ультрафіолетового опромінення композицій на попередній стадії формування матеріалів на фізико-механічні, теплофізичні властивості, корозійну і зносостійкість захисних покриттів. З метою визначення та оптимізації складу покриттів і режимів магнітної обробки, ультразвукового та ультрафіолетового опромінення, а також прогнозованого регулювання структури та властивостей гетерогенних матеріалів передбачено розробити та обґрунтувати механізм керування взаємодією на межі розділу фаз «основа – полімеркомпозитне покриття».
Виходячи з мети діяльності для створення полімерних композитів та захисних покриттів на їх основі у Лабораторії функціонує новітнє устаткування для дослідження у комплексі властивостей матеріалів:
- адгезійні та залишкові напруження;
- фізико-механічні;
- теплофізичні;
- аналіз структури полімерних композитів;
- експлуатаційні (коефіцієнт тертя, гідроабразивне зношування, корозійна стійкість).
АДГЕЗІЙНА МІЦНІСТЬ ТА ЗАЛИШКОВІ НАПРУЖЕННЯ
Адгезійна міцність. Досліджували вплив вмісту наповнювачів різної природи і дисперсності на адгезійні властивості покриттів до металевої основи, вимірюючи руйнівне напруження («метод грибків») при рівномірному відриві пари склеєних зразків згідно з ГОСТ 14760-69 (рис. 1, рис. 2). Дослідження адгезійної міцності при зсуві проводили згідно з ГОСТ 14759-69, аналогічно вимірюючи силу відривання клейових з’єднань стальних зразків (рис. 3) на автоматизованій розривній машині УМ-5 при швидкості навантаження υ = 10 Н/с. Діаметр робочої частини стальних зразків при відриві становив – d = 25 мм. Слід зазначити, що площа склеювання зразків, які досліджували при відриві та зсуві, була однаковою.
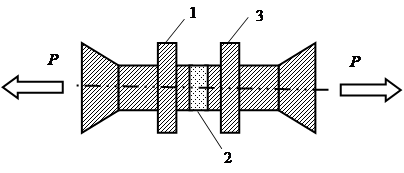
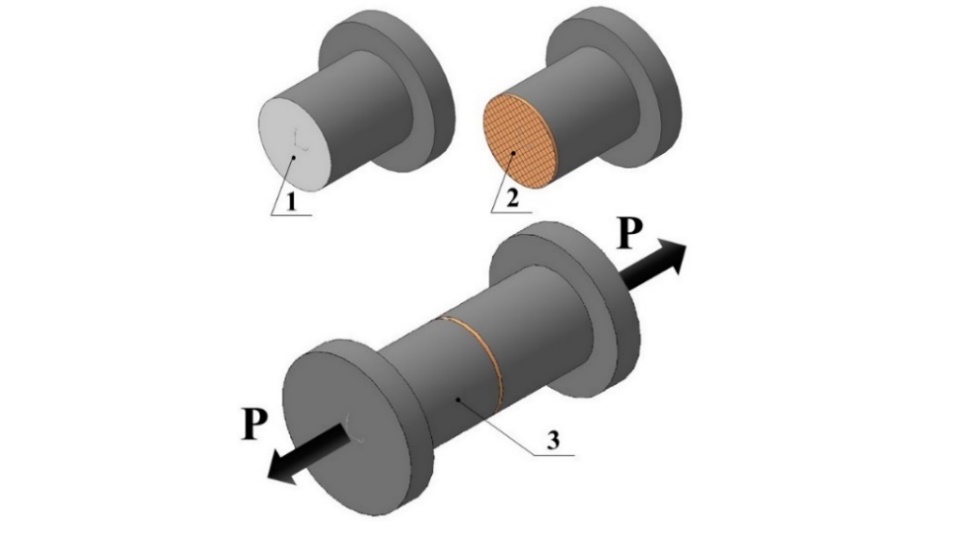
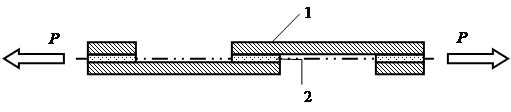
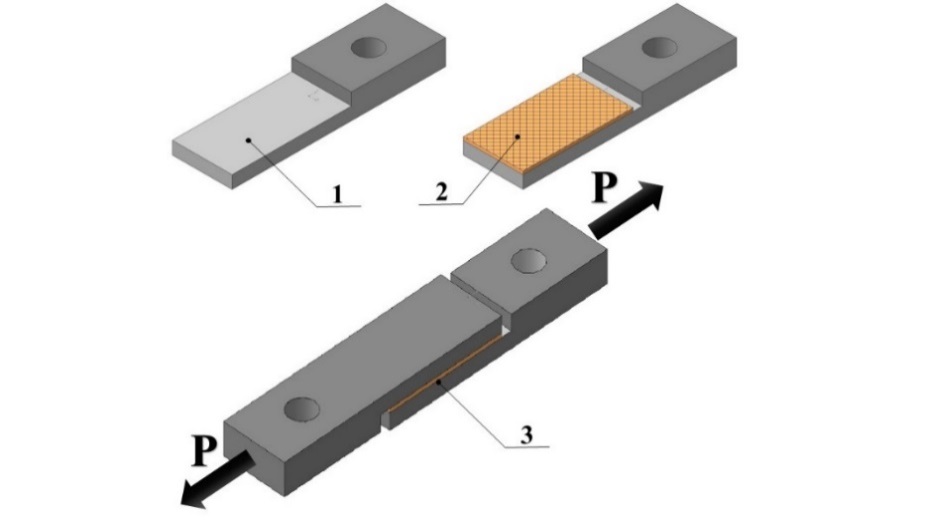
Дослідження залишкових напружень. Залишкові напруження у КМ визначали консольним методом. Величину σз визначали за формулою:
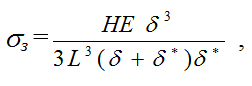
де: Н – відхилення основи від початкового положення, м; Е – модуль пружності основи (Е = 2,1 × 108 Па); L – довжина основи з покриттям, м; δ – товщина основи, м; d *– товщина покриття, м.
Покриття товщиною δ = 0,1…0,2 мм формували на стальній основі. Параметри основи: загальна довжина – l = 100 мм; робоча довжина – l0 = 80 мм; товщина – δ = 0,2 мм. У процесі зшивання на межі поділу фаз «захисне покриття – металева основа» утворюються фізичні і хімічні зв’язки, що зумовлює виникнення залишкових напружень розтягу та відхилення консолі (у вигляді основи з покриттям), абсолютне значення якого (Н) визначали у кінці дослідження (після полімеризації матеріалу впродовж часу τ = 72 год) (рис. 4).
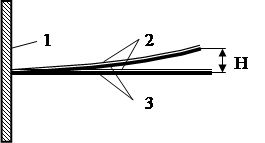
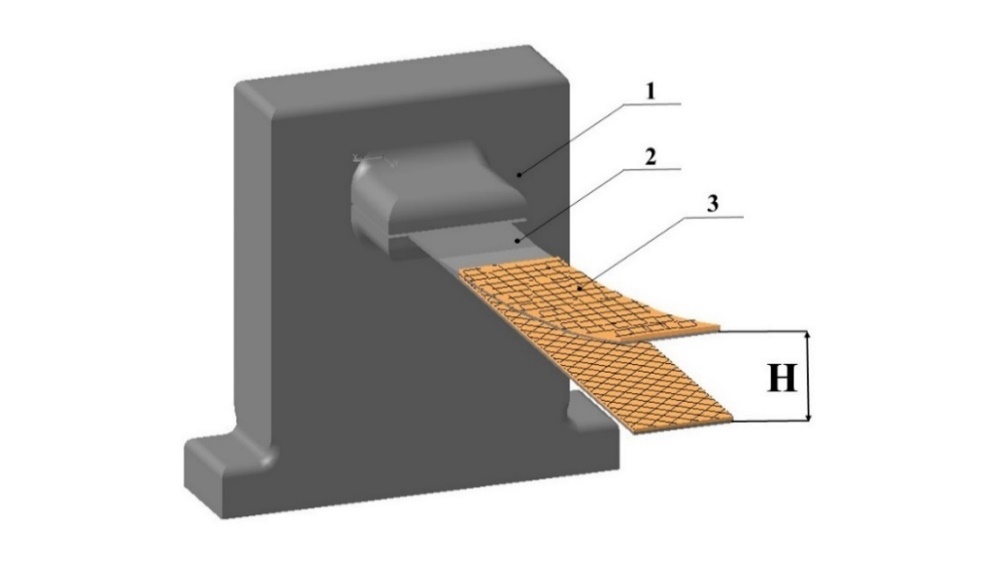
ФІЗИКО-МЕХАНІЧНІ ВЛАСТИВОСТІ
У Лабораторії розроблено установку для дослідження міцності полімерних матеріалів до втоми. Зразки витримували під попередньо вибраним навантаженням впродовж 1500 год і визначали його прогин, що свідчить про динаміку когезійних властивостей відомих і розроблених композитів. Додатково випробовували матеріали на циклічну втому за рахунок повторного зняття і додавання навантаження. У результаті цього аналізували величину пружної і пластичної деформації у зразках.
Установка для дослідження втомної міцності композитів (дослідження проводить к.т.н., доцент, доцент кафедри експлуатації суднових енергетичних установок Богдан Ю.О.)
Реологічні властивості. Такі експерименти є важливим джерелом відомостей про технологічні властивості композицій, їх структуру, взаємодію часток зі зв’язувачем та стан їх поверхні. Найбільш поширеним реологічним показником, що характеризує особливості перебігу полімерних композицій, є їх в’язкість.
Реологічні властивості полімерних композицій визначали за допомогою ротаційного віскозиметра «Brookfield» (ГОСТ 25271-93), а також (ІСО 2555-89). Принцип роботи приладу заснований на обертанні вимірювального шпинделя, зануреного в тестовану композицію. Збір даних проводили в автоматичному режимі за допомогою комп’ютера зі встановленим програмним забезпеченням Brookfield Rheocalc32. Визначали середню динамічну в’язкість (η) в інтервалі температур від 25 до 90 ºС при одній і тій же швидкості обертання шпинделя. Додатково визначали температуру композицій, значення якої виводили на екран за допомогою датчика температури RTD.
ТЕПЛОФІЗИЧНІ ВЛАСТИВОСТІ
Для дослідження впливу природи зв’язувача і наповнювачів на термічні перетворення у композитах застосовували метод термогравіметричного (ТГА) і диференціального термічного аналізу (ДТА), використовуючи дериватограф «Thermoscan-2». Дослідження проводили у температурному діапазоні ∆Т = 298…773 К, використовуючи кварцові тиглі для зразків об’ємом V = 0,5 см3. Під час дослідження швидкість підйому температури становила υ = 10 К/хв, при цьому як еталонну речовину використовували Al2O3 (m = 0,5 г).
Додатково у Лабораторії досліджують наступні теплофізичні властивості полімерних композитів.
1. Теплостійкість (за Мартенсом). Теплостійкість визначали відповідно до ГОСТ 21341-75 (ISO 75-2). Методика експериментальних випробувань полягає у визначенні температури, за якої зразок деформується на задану величину (hд = 6 мм) внаслідок нагрівання зі швидкістю υт = 3 К/хв під дією постійного згинаючого навантаження F = 5 ± 0,5 МПа.
2. Термічний коефіцієнт лінійного розширення (ТКЛР). ТКЛР та температуру склування Тс зразків розраховували за кривою залежності відносної деформації від температури, апроксимуючи цю залежність експоненціальною функцією відповідно до ГОСТ 15173-70 (ISO 11359-2). Відносну деформацію визначали за зміною довжини зразка при підвищенні температури.
АНАЛІЗ СТРУКТУРИ ПОЛІМЕРНИХ КОМПОЗИТІВ
Для кращого змочування та рівномірного розподілу у об’ємі полімерних композицій нано- (фулірен, нанотрубки, графен, наноалмаз та ін.) і мікродисперсних наповнювачів проводили ультразвукову обробку (УЗО) композицій впродовж експериментально визначених режимів (тривалість τ = 1,5 ± 0,1 хв, частота коливань хвилеводу v = 22 кГц).
Інфрачервона спектроскопія. Для визначення природи хімічних зв’язків, які виникають при структуроутворенні композитів, використано метод ІЧ-спектроскопії. ІЧ-спектри досліджували на спектрофотометрі марки «IRAffinity-1» (Японія) у області частот 400…4000 см-1 однопроменевим методом у відбитому світлі. Хвильові числа визначали за допомогою комп’ютерної програми IRsolution.
Якісний аналіз ІЧ-спектрів проводили за законом Ламберта-Бера, враховуючи при цьому значення оптичної густини (D) і напівширини (b) смуг поглинання на спектрах композитів. При розшифруванні спектрів враховували хімічний склад макромолекул полімеру і наповнювачів. Аналізували ІЧ-спектри матриці, наповнювачів та композитів.
ЕПР-спектроскопія. Додатково досліджували наявність фізичних зв’язків і ступеня зшивання матеріалів методом електронного парамагнітного резонансу. ЕПР-спектри досліджували на спектрометрі марки «СМS-8400». При аналізі ЕПР-спектрів за допомогою програми «EPR Commander 4.0» визначали наступні характеристики: ширина (розраховується, як різниця між величинами магнітного поля у точках мінімуму і максимуму спектру),інтенсивність (максимальна різниця амплітуд на фрагменті), концентрація парамагнітних центрів (розрахунок подвійного інтегралу фрагмента). Аналіз даних параметрів дозволяє констатувати про когезійну міцність матеріалів.
ЕКСПЛУАТАЦІЙНІ ВЛАСТИВОСТІ
(КОЕФІЦІЄНТ ТЕРТЯ, ГІДРОАБРАЗИВНЕ ЗНОШУВАННЯ, КОРОЗІЙНА СТІЙКІСТЬ)
Зносостійкість в умовах тертя. Трибологічні властивості матеріалів досліджували на випробувальній машині 2070 СМТ-1 за схемою «диск-колодка» і методикою відповідно до ГОСТ 23.224-86 (ASTM G77 – 17).
Масову інтенсивність зносу визначали за формулою:

де: ∆m – різниця маси зразка до і після тертя, мг; ∆L – шлях тертя, км.
Коефіцієнт тертя розраховували відповідно до ГОСТ 11629-75 (ASTM G77–17) за формулою:

де: М – середньоарифметичне значення моменту тертя, Н × м;
F – навантаження на колодку, Н;
r – радіус металевого контртіла (плеча), м.
Диск (контртіло) виготовляли з матеріалу сталь 45, термообробленої до твердості 45…48 НRС і з шорсткістю поверхні Ra = 0,16…0,32 мкм.
Дослідження проводили в умовах сухого тертя, впливу морської води (середня солоність 35 ‰) та в мастильного середовища при питомому навантаженні p = 1 МПа і швидкості ковзання υ = 1,0 м/с. Шлях ковзання зразків при випробуваннях становив 10 000 м.
Температуру у області контакту визначали за допомогою термопари «хромель-копель», сигнал від якої реєстрували вимірювальною апаратурою. Розташовували термопару на відстані lт = 2 мм від області контакту зразка з контртілом.
Гідроабразивна стійкість. Відносну стійкість композитів до дії гідроабразиву визначали з використанням відцентрового прискорювача (ГОСТ 23201-78). Методика дозволяє моделювати реальні процеси зношування деталей механізмів під дією гідроабразиву. Як гідроабразивну суспензію використано суміш технічної води і абразивних часток кварцового піску (5:1 за об’ємом). Випробування зразків проводили при зміні кута атаки гідроабразивної суміші в межах від å = 30° до å = 90°.
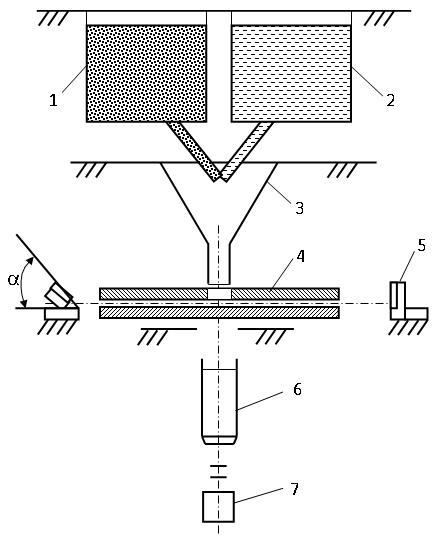
Відносну інтенсивність зношування визначали за формулою:
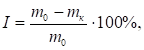
де: m0– маса зразка на початку дослідження, кг; mк – маса зразка у кінці дослідження, кг.
Коефіцієнт зносостійкості визначали за формулою:

де: ІЕ – відносна інтенсивність зношування еталону (сталь Ст 3) %; І– відносна інтенсивність зношування КМ, %.
Корозійна стійкість. Корозійну стійкість захисних покриттів досліджували методом імпедансної спектроскопії, в результаті чого аналізували зміну опору і ємності зразків у часі під впливом агресивних середовищ. Для вимірювання опору і ємності захисних покриттів використовували прилад RCL-метр типу Е7-22. Прилад під’єднували до вимірювальної комірки, у яку поміщали зразки у вигляді покриттів, нанесених на металеву основу. На покриття наклеювали скляні циліндри з діаметром d = 25 мм, які заповнювали дистильованою водою (ТУУ 006: 2011). Упродовж 365 діб вимірювали опір і ємність покриттів, значення яких перераховували за формулами: Rкор = R∙S, кОм;
Скор = С∙S, пФ; S = πD2/4, см2.
Додатково корозійну стійкість досліджували у природних умовах, витримуючи зразки у агресивних середовищах морської та річкової води. У результаті аналізували наявність тріщин у зразках, відшарування покриттів та зміну їх маси.
РОЗРОБЛЕНЕ АВТОМАТИЗОВАНЕ ОБЛАДНАННЯ ДЛЯ ДОСЛІДЖЕННЯ ТЕПЛОФІЗИЧНИХ ТА МЕХАНІЧНИХ
ВЛАСТИВОСТЕЙ ПОЛІМЕРНИХ КОМПОЗИТІВ
Виходячи з мети діяльності та поставлених завдань дослідження для створення полімерних композитів та захисних покриттів на їх основі у Лабораторії функціонує новітнє розроблене нами устаткування для дослідження теплофізичних та механічних властивостей матеріалів:
– розроблений автоматизований комплекс з програмним забезпеченням для дослідження теплофізичних властивостей (термічний коефіцієнт лінійного розширення, температура склування) полімерних композитів;
– розроблений автоматизований комплекс з програмним забезпеченням для дослідження механічних властивостей (руйнівні напруження і модуль пружності при згинанні) полімерних композитів.
РОЗРОБЛЕНИЙ АВТОМАТИЗОВАНИЙ КОМПЛЕКС З ПРОГРАМНИМ ЗАБЕЗПЕЧЕННЯМ ДЛЯ ДОСЛІДЖЕННЯ ТЕПЛОФІЗИЧНИХ ВЛАСТИВОСТЕЙ (ТЕРМІЧНИЙ КОЕФІЦІЄНТ ЛІНІЙНОГО РОЗШИРЕННЯ, ТЕМПЕРАТУРА СКЛУВАННЯ) ПОЛІМЕРНИХ КОМПОЗИТІВ
У Лабораторії «Полімеркомпозитні матеріали в суднобудуванні» розроблено автоматизований комплекс, що відповідає сучасним вимогам дослідження полімерних композитів в умовах впливу теплового поля, схема якого зображена на рис. 1.
Комплекс складається з механічної частини, вимірювального і блоку приладів. Механічна частина включає нагрівальні модулі. Кожен модуль має керамічну підставку 2 з направляючими 3 для центрування зразків і циліндричну електричну піч опору 4. Функцію охолоджувача виконують вентилятори (кулери) поміщені в дифузори, пригвинчені на задній внутрішній стінці приладу, які відбирають частину теплового потоку від печей електричного опору.
На мікропроцесор 37 припадають сервісні і високорівневі функції управління приладом, що автоматизують робочий процес і роблять прилад автономним, не вимагає для цього управління ззовні. На частку персонального комп’ютера (ПК) 39 покладені інтерфейсні функції. До нього приєднані датчики переміщення через USB роз’єм, а також мікропроцесор, через який надходить сигнал від термопар, що реєструють температуру в печах. Це дозволяє визначати ТКЛР матеріалів, ґрунтуючись на вимірюванні зміни довжини і температури досліджуваних зразків. Виходячи з цього, нами був розроблений алгоритм автоматизації роботи приладу (рис. 2), який дозволяє спростити і прискорити роботу над експериментом.
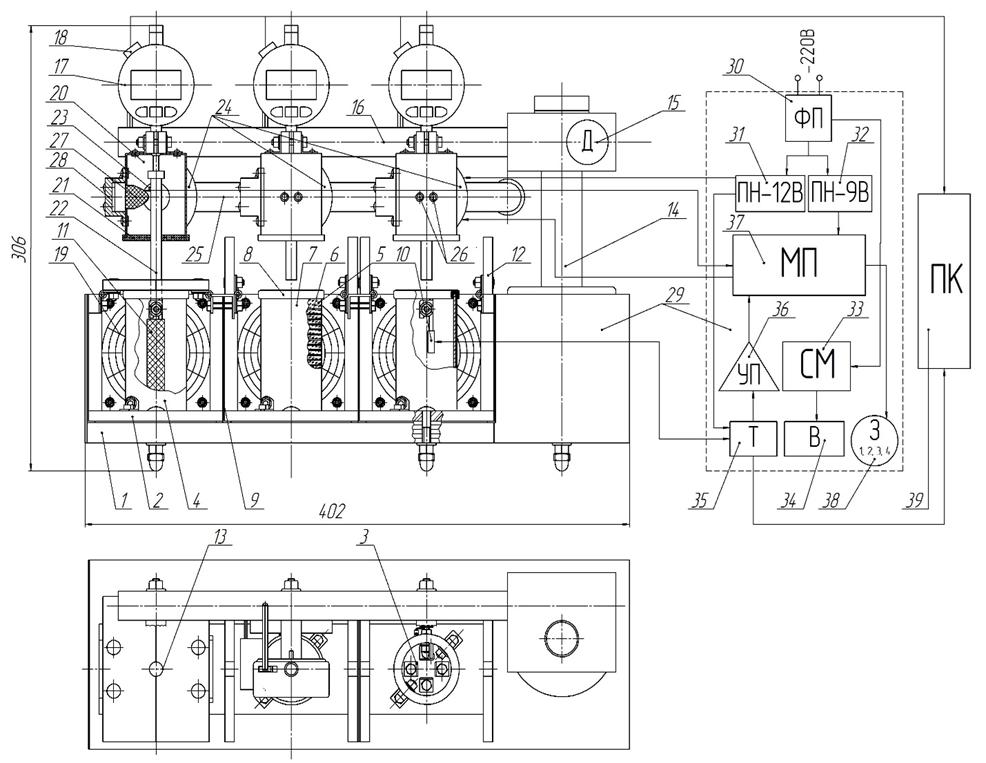
1 – монтажна плита; 2 – керамічна основа; 3 – направляючі; 4 – електрична піч опору; 5 – внутрішня електроізоляція; 6 – фехралева спіраль; 7 – зовнішня термоелектроізоляція; 8 – кільцева прокладка; 9 – стінка; 10 – датчик температури ДТ-3Д; 11 – зразок; 12 – подвійні половинчасті кришки; 13 – на-півкруглий наскрізний отвір; 14 – стійка; 15 – електромотор; 16 – рухома консоль; 17 – електронний цифровий індикатор переміщення; 18 – USB роз’єм для виходу даних; 19 – вентилятор охолодження (кулер); 20 – камера-димозбірник (димовідвідна камера); 21 – ущільнювач з тепло- електроізолюючого матеріалу; 22 – кварцова трубка; 23 – отвір для виходу диму; 24 – відвідний колектор; 25 – патрубок для відводу диму; 26 – світло-діодні індикатори (зелений, червоний); 27 – датчик газу, диму, MQ-2 для Arduino PIC ARM; 28 – захисний кожух датчика; 29 – приборний блок; 30 – фільтр перешкод; 31 – конвертер напруги 12В; 32 – конвертер напруги 9В; 33 – силовий модуль (регулятор напруги); 34 – цифровий вольтметр змінного струму; 35 – температурний цифровий індикатор; 36 – підсилювач-конвертер сигналів; 37 – мікропроцесор; 38 – зумер; 39 – персональний комп’ютер.
Вимірювальний дилатометричний автоматизований комплекс працює наступним чином. У електричні печі встановлюють зразки, які зверху закривають кришками. Потім вмикають установку. За допомогою регульованого силового модуля встановлюють необхідну швидкість нагріву, через електричну напругу, дані про що висвічуються на цифровому вольтметрі змінного струму. Таким чином запускаємо нагрів.
Нагрівання. Разом з нагріванням запускають процес зчитування даних за допомогою датчиків температури ДТ-3Д при температурному режимі внутрішнього середовища печей, де розташовані зразки. Операція має циклічний характер і буде повторюватися до тих пір, поки не буде виконана умова, а саме – не буде досягнута наперед задана температура – Tmax = 200 °C, що є останньою сходинкою циклу нагрівання.
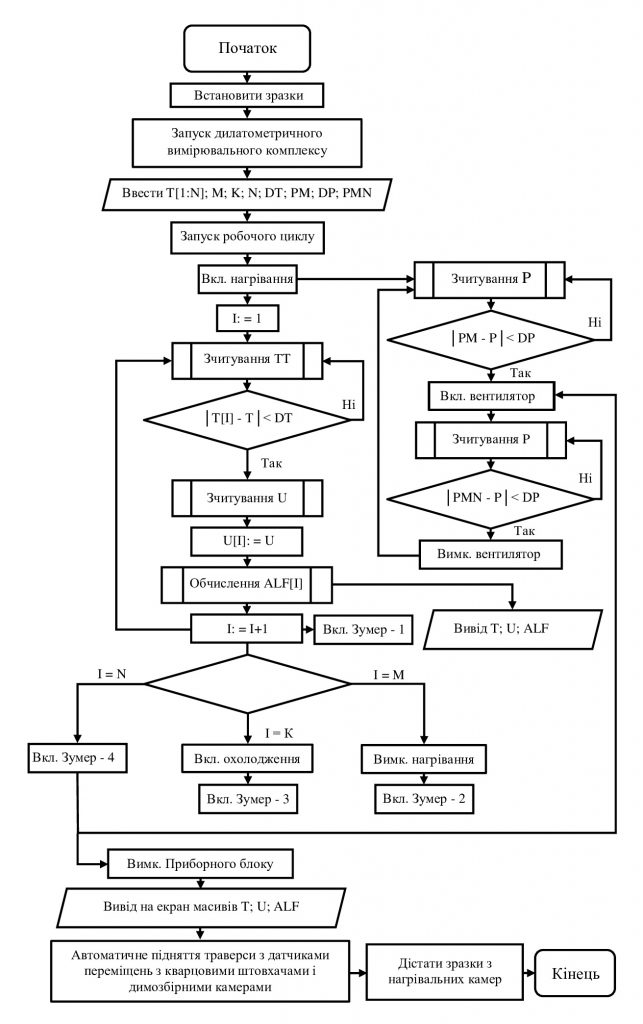
Охолодження. Коли температура в процесі нагрівання досягає максимального заданого значення, нагрів автоматично вимикається. Алгоритм роботи та характер процесу зчитування даних залишається тим же, що і при нагріванні. Слід зауважити, що на початку процесу охолодження електричні печі опору відносно рівномірно охолоджуються самі по собі, віддаючи тепло у зовнішнє середовище, таким чином досягаючи термодинамічної рівноваги. Однак, зі зниженням температури в процесі охолодження цей процес все більше сповільнюється через теплову інерційність складальних одиниць приладу. З метою прискорення охолодження і надання йому більш рівномірного характеру нами була задіяна система охолодження з використанням кулерів, яка автоматично вмикається у діапазоні температур – Т = 100 ± 5 °C.
Автоматичне вимкнення блоку приладів. При охолодженні камери до мінімальної температури, передбаченої програмою вимірювань, відбувається короткочасне вмикання вентиляторів для фінального очищення димовідвідної камери від залишків диму і газів, а потім виконується повне відключення блоку приладів.
За допомогою розробленого комплексу проводили експерименти з метою отримання дилатометричних кривих для оцінювання ТКЛР і температури склування композитів
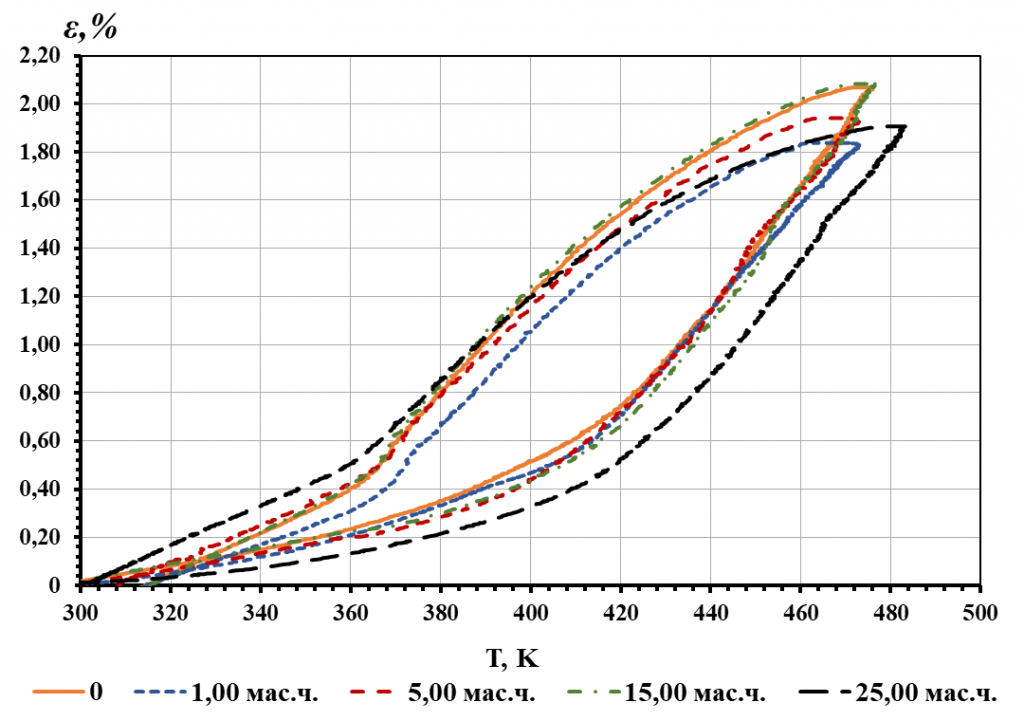
РОЗРОБЛЕНИЙ АВТОМАТИЗОВАНИЙ КОМПЛЕКС З ПРОГРАМНИМ ЗАБЕЗПЕЧЕННЯМ ДЛЯ ДОСЛІДЖЕННЯ МЕХАНІЧНИХ ВЛАСТИВОСТЕЙ (РУЙНІВНІ НАПРУЖЕННЯ І МОДУЛЬ ПРУЖНОСТІ ПРИ ЗГИНАННІ) ПОЛІМЕРНИХ КОМПОЗИТІВ
Показники руйнівних напружень і модуля пружності при згинанні полімерних композитів визначали за допомогою розробленого автоматизованого комплексу згідно з ГОСТ 4648-71 (ASTM D 790–03) і ГОСТ 9550-81 (ASTM D 790–03) відповідно. Використовували схему чотириточкового згинання, вимірюючи при цьому відносну деформацію зразків залежно від сили навантаження, яку задавали автоматично кроковим двигуном. Комплекс обладнаний датчиками деформації і навантаження, які у автоматичному режимі фіксували динаміку даних, що записували в процесі експерименту на ПК. Зазначимо, що для автоматизованої реєстрації результатів дослідження на ПК нами розроблено програмне забезпечення, яке додатково забезпечує обробку даних і побудову кривих деформації як остаточний результат експерименту. На завершальному етапі за отриманими кривими розраховували показники модуля пружності і руйнівних напружень при згинанні розроблених та відомих матеріалів.
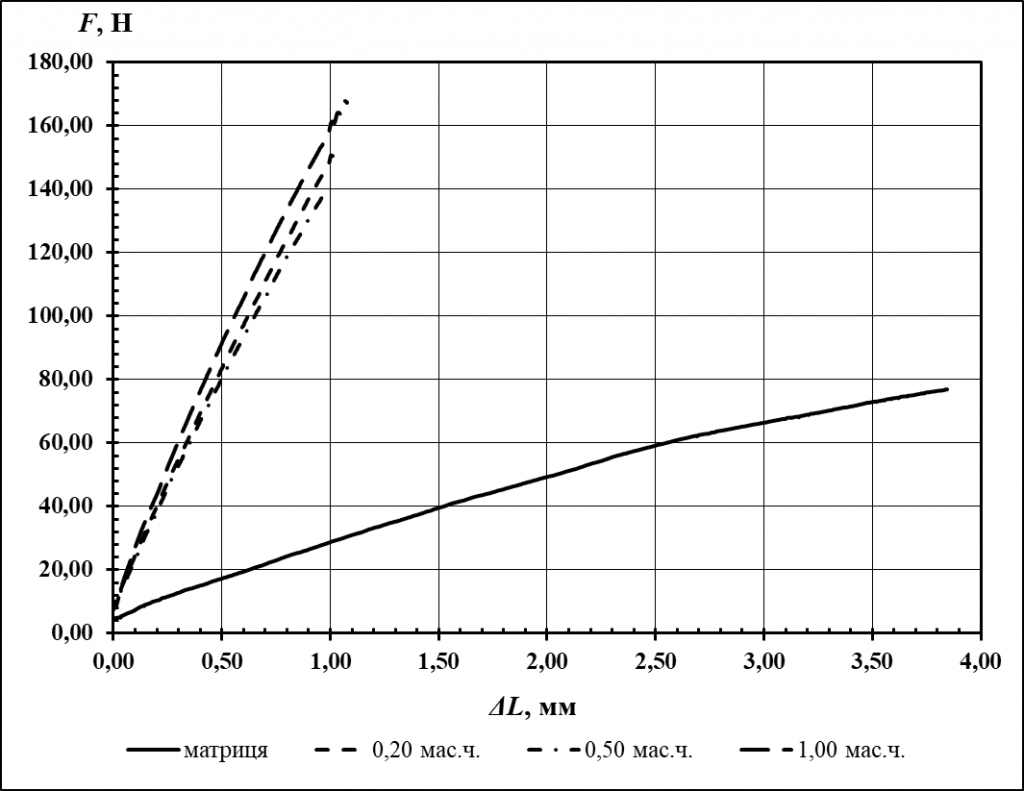
Можна констатувати, що у Лабораторії «Полімерні композитні матеріали у суднобудуванні» розроблено автоматизоване обладнання для дослідження теплофізичних та механічних властивостей полімерних композитів. Це дозволяє з одного боку суттєво зекономити час на проведення експериментів та обробку результатів дослідження, а з іншого боку – досліджувати з високою достовірністю у комплексі властивості полімерних композитів з наперед заданими і прогнозованими властивостями.
Продукт
На основі проведених досліджень та отриманих результатів створено нові композитні матеріали та покриття на їх основі з прогнозованими експлуатаційними характеристиками для захисту технологічного обладнання від корозії та зносу.
а) | б) |
Аналіз корозійного руйнування палубних механізмів судна «Олесь Гончар»
Розроблено нові матеріали, методи і способи підвищення корозійної стійкості та зносостійкості захисних покриттів, що мають пріоритетний характер і захищені патентами України. Багатошарові покриття на основі епоксикомпозитних матеріалів забезпечують високі показники працездатності і придатні для захисту поверхонь конструктивних елементів механізмів від впливу агресивних середовищ і гідроабразиву.
Впровадження результатів розробок можливо на всіх суднобудівних заводах Херсонської області, що займаються питаннями випробування елементів конструкцій, аспектами підвищення антикорозійних характеристик і зносостійкості технологічного обладнання. Крім того, впровадити результати роботи можливо на підприємствах хімічної, харчової, нафтопереробної, радіолокаційної промисловості та машинобудування з метою збільшення ресурсу роботи обладнання.


Патенти України на корисні моделі, отримані колективом лабораторії
Проблема і можливість
Сьогодні недостатньо уваги приділено розробці нових наноепоксикомпозитів при модифікації як інгредієнтів, так і композицій, зовнішніми енергетичними полями на початкових стадіях їх формування. Це відкрило принципово нові можливості у створенні нових захисних покриттів з підвищеними характеристиками. Тому дослідження процесів зшивання епоксикомпозитів під впливом магнітного поля, ультразвукового та ультрафіолетового опромінення для поліпшення експлуатаційних характеристик захисних покриттів є актуальним завданням сучасного матеріалознавства.
Перевагою розробок над зарубіжними й вітчизняними аналогами є облік основних факторів агресивних середовищ, де експлуатується технологічне обладнання, а також розробка матеріалів, які у комплексі мають високі показники фізико-механічних, теплофізичних властивостей, корозійної та зносостійкості. Технологічний процес формування полімерних композитних матеріалів відповідає стану подібних технологій, які розробляються науково-дослідними інститутами Білорусі, Прибалтики, Німеччини, США, Китаю та Японії.
Усі інгредієнти композитних матеріалів і захисних покриттів на їх основі (епоксидна смола, пластифікатори, наповнювачі) є в наявності на території України. При цьому такі дисперсні наповнювачі, як червоний і коричневий шлами, газова сажа, ферит є відходами промислових підприємств, що дозволяє стверджувати про економічну ефективність впровадження нових матеріалів.
Крім того, співробітниками Херсонської державної морської академії розроблено та є в наявності технологічне обладнання (установка для магнітної, ультразвукової модифікації та ультрафіолетовий випромінювач) для обробки олігомерних композицій зовнішніми енергетичними полями.
Пропозиції щодо впровадження
Впровадження покриттів на підприємствах забезпечить: підвищення корозійної стійкості обладнання у 2,5…2,7 разів, підвищення стійкості до зношування у 2,0…2,2 рази, збільшення міжремонтного періоду роботи у 3,0…3,5 разів.
Впровадження результатів розробки можливо на усіх суднобудівних заводах Херсонської області, що займаються питаннями випробування елементів конструкцій, аспектами підвищення антикорозійних характеристик і зносостійкості технологічного обладнання. Крім того, впровадити результати роботи можливо на підприємствах хімічної, газотранспортної, нафтопереробної, радіолокаційної промисловості та машинобудування з метою збільшення ресурсу роботи обладнання.